An aircraft manufacturing company uses CAE software for aircraft-aided design. Because many of the CAE documents are relatively large, leading to different personnel or design personnel to report the design results to higher levels, the approval uses only the same CAE model for communication. The version management of CAE design files will become a bottleneck for improving R&D efficiency.
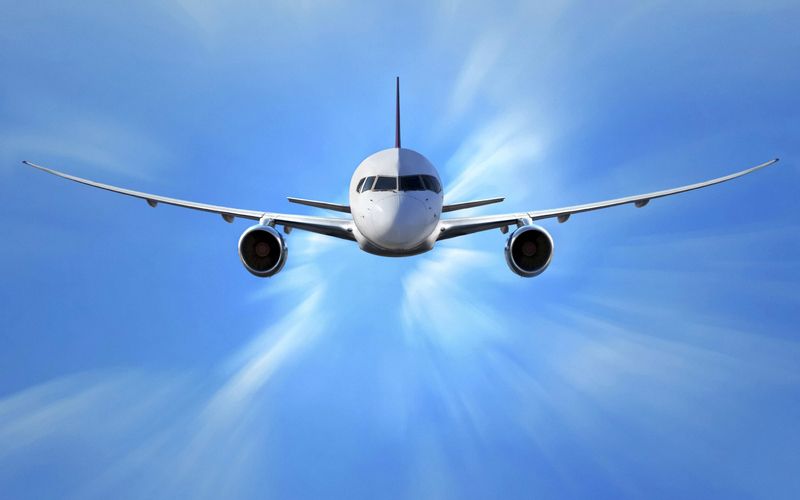
CAE technology can effectively shorten the development cycle and save development costs. It has become an indispensable and crucial design method in the design of different aircraft types. Since the 1990s, China has gradually applied CAE technology to the development of different aircraft types, and has gradually gained understanding and support from relevant designers. At present, China’s aerospace design departments almost all have their own CAE technical personnel, and their technology is also getting higher and higher. In the current aerospace field, the proportion of CAE technology in design is increasing, the calculation scale is increasing, the complexity is increasing, and the disciplines are intertwined.
Aircraft generally consist of wings, fuselage, landing gear and aircraft operating systems, and their structure is complex. The traditional design and processing of space shuttles are based on the two-dimensional engineering drawings. The accuracy of processed product data is not high, and product designs are often constantly modified. Therefore, its development cycle is long and costs are high.
With the use of a large number of engineering application software, CAE can perform routine structural analysis, thermal analysis, dynamic analysis, etc. on major components of aircraft such as fuselage, wing, rudder surface, engine nacelle, airtight cabin, landing gear, etc. In addition, fluid-solid coupling, thermal-structure coupling, and aerodynamic analysis can also be performed to fully meet the requirements for finite element analysis in aircraft design.
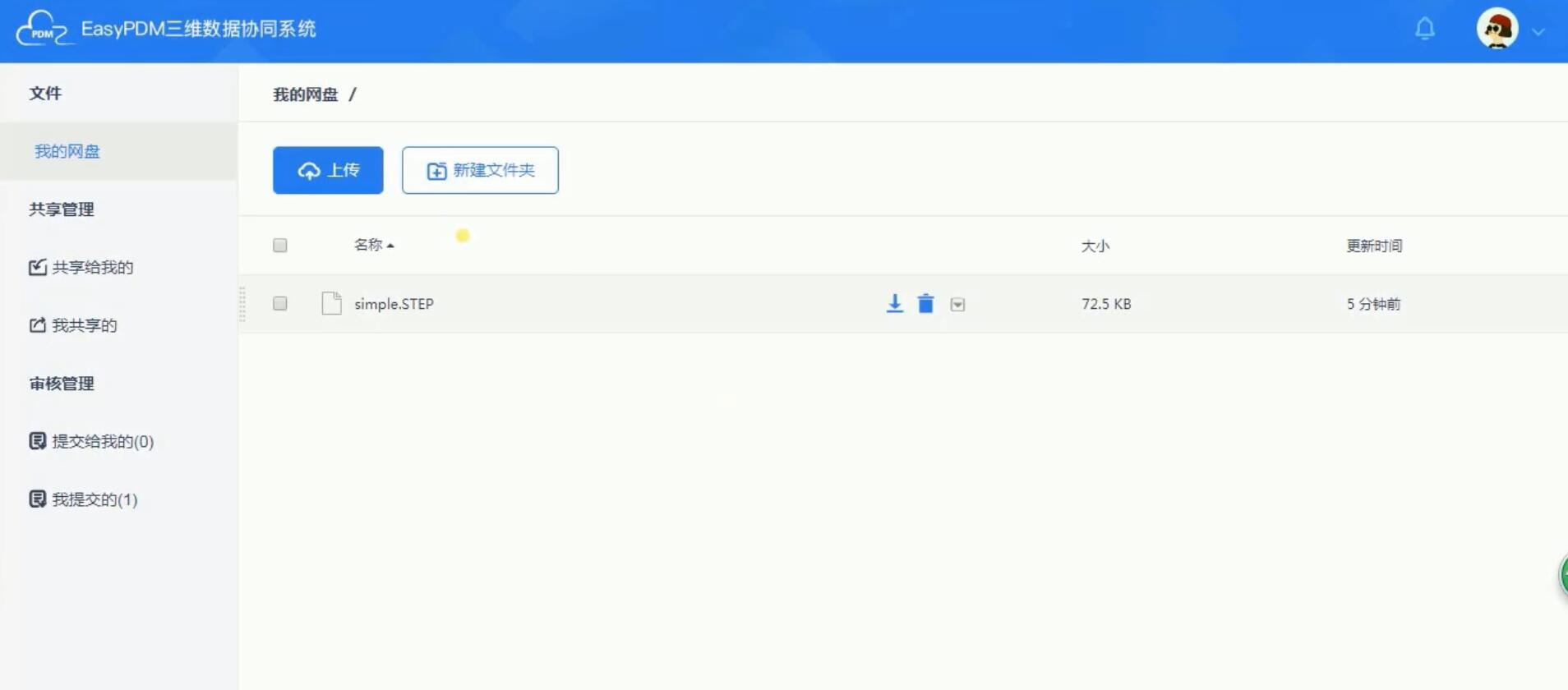
An aircraft manufacturing company uses CAE software for aircraft-aided design. Because many of the CAE documents are relatively large, leading to different personnel or design personnel to report the design results to higher levels, the approval uses only the same CAE model for communication. The version management of CAE design files will become a bottleneck for improving R&D efficiency.
Simright provided the private cloud deployment of EasyPDM, including some custom development, that effectively solved these problems.
EasyPDM can be used to manage the CAD/CAE 3D models. It mainly includes three types of functions: document collaboration, document version management, and the display of the CAD/CAE 3D model. It does not use the traditional version management system ideas. However, according to the shared folder, @ mechanism and version comment mechanism, it achieve the above three types of functions.
Its main function has three aspects.
Teamwork: Document version management, file modification approval, and event notifications make collaboration more fluid.
3D Model Viewing: View many commercial CAE/CAD models.
Common tools for 3D models: model volume/surface area calculations, dimensional measurements, 3D model comparisons, etc.
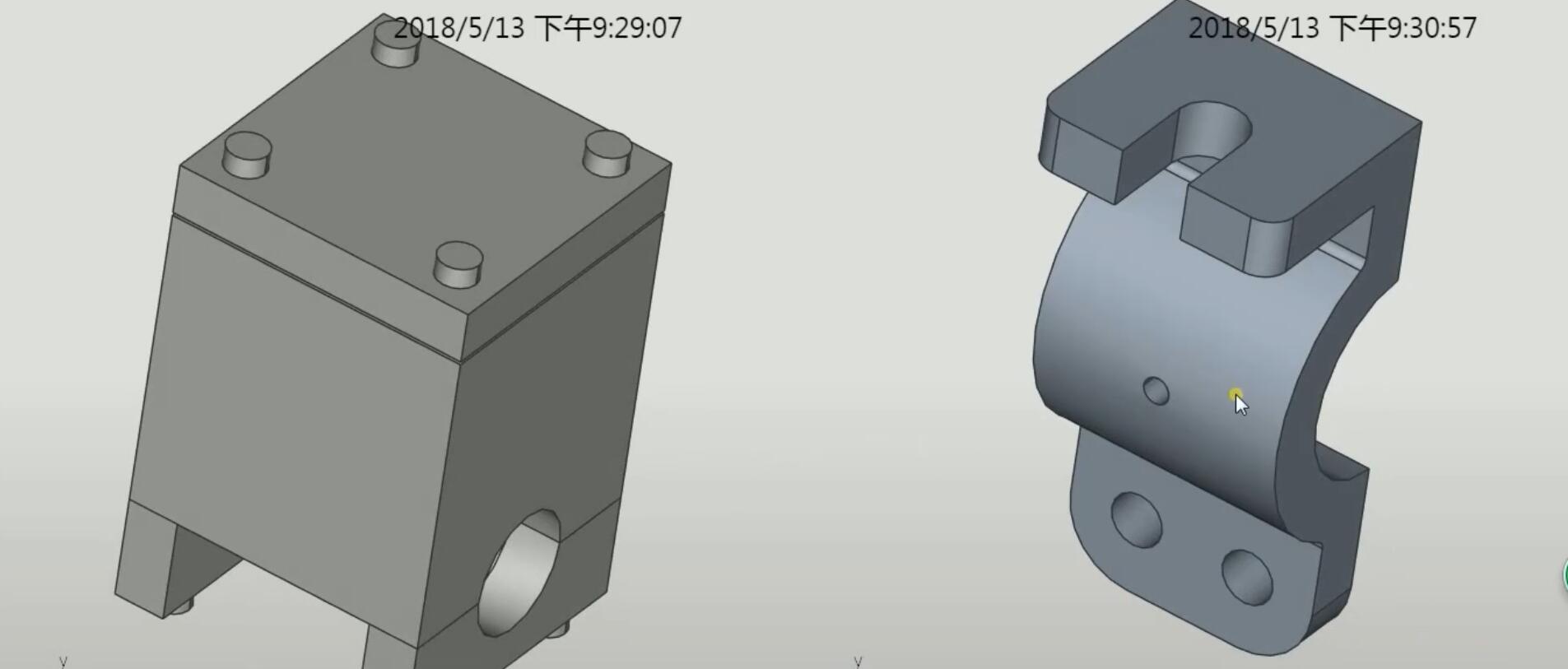